
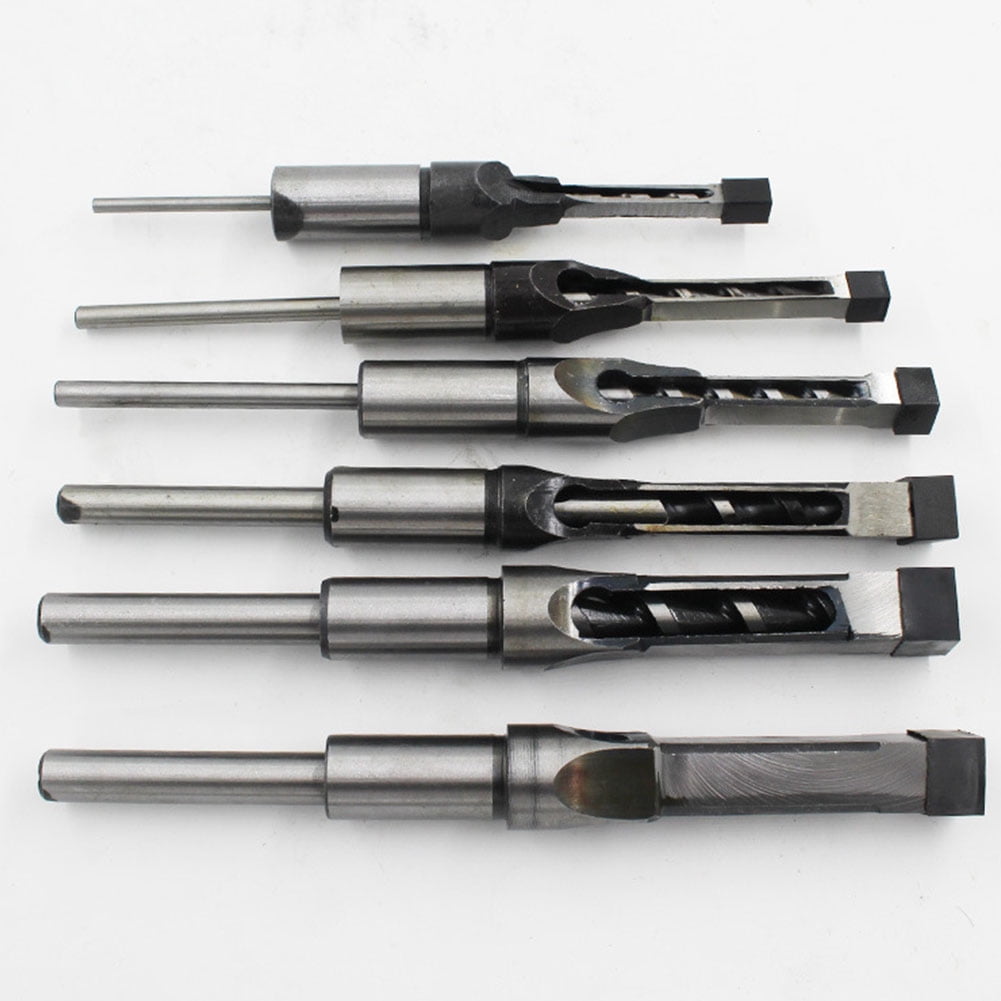
If they are overheated (e.g., by frictional heating while drilling) they lose their temper, resulting in a soft cutting edge.

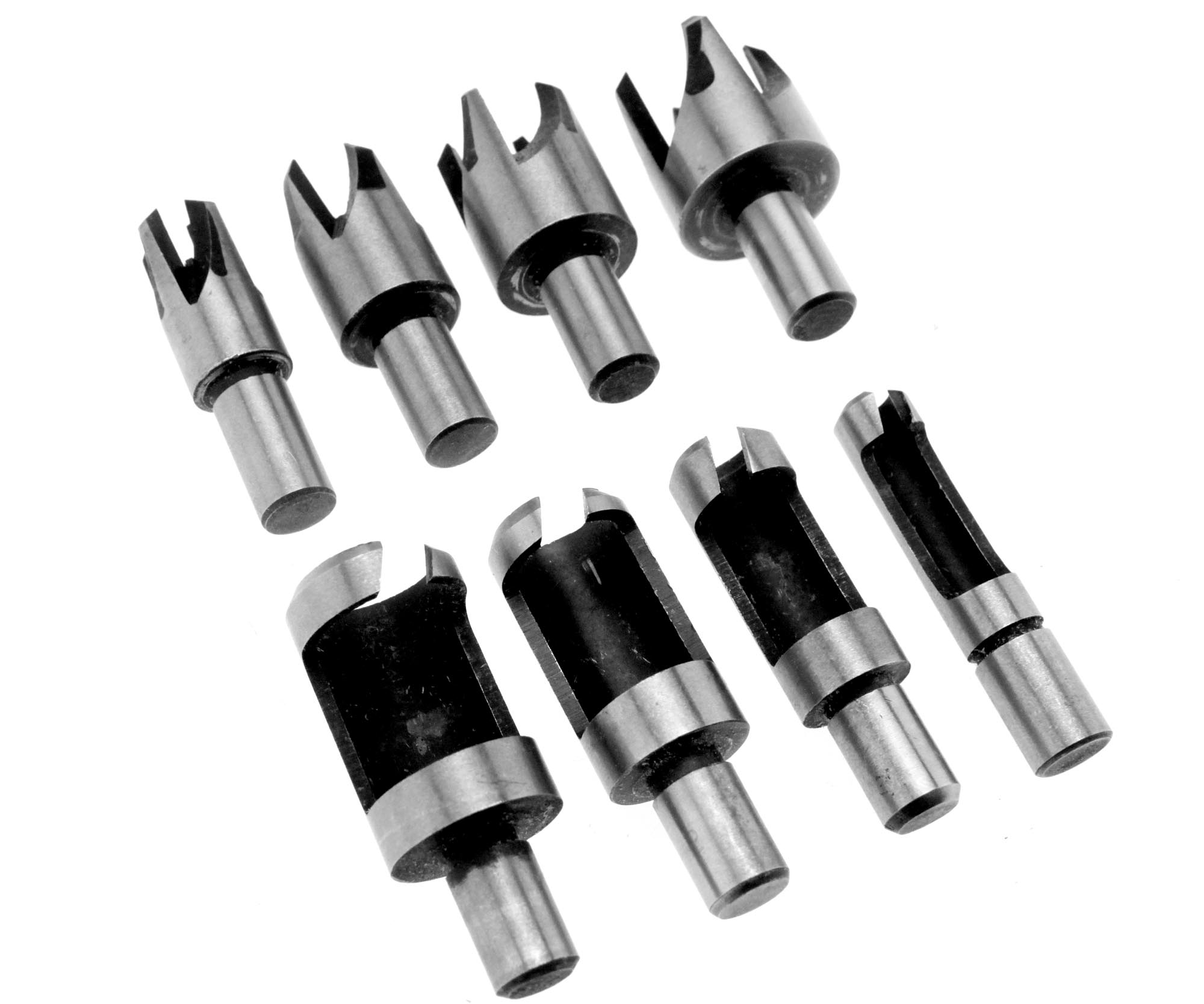
The diameter-to-length ratio of the drill bit is usually between 1:1 and 1:10. Other types of shank used include hex-shaped, and various proprietary quick release systems. For heavy duty drilling in industry, bits with tapered shanks are sometimes used. Most drill bits for consumer use have straight shanks. Twist drill bits are available in standard lengths, referred to as Stub-length or Screw-Machine-length (short), the extremely common Jobber-length (medium), and Taper-length or Long-Series (long). While longer bits can drill deeper holes, they are more flexible meaning that the holes they drill may have an inaccurate location or wander from the intended axis.

The functional length of a bit determines how deep a hole can be drilled, and also determines the stiffness of the bit and accuracy of the resultant hole.A very acute point angle has more web surface area presented to the work at any one time, requiring an aggressive lip angle, where a flat bit is extremely sensitive to small changes in lip angle due to the small surface area supporting the cutting edges. The proper amount of lip clearance is determined by the point angle. Both conditions can cause binding, wear, and eventual catastrophic failure of the tool. A greater lip angle will cause the bit to cut more aggressively under the same amount of point pressure as a bit with a smaller lip angle. The lip angle determines the amount of support provided to the cutting edge.The correct point angle for the hardness of the material influences wandering, chatter, hole shape, and wear rate. Harder materials require a larger point angle, and softer materials require a sharper angle. The point angle, or the angle formed at the tip of the bit, is determined by the material the bit will be operating in.Low spiral (low twist rate or "elongated flute") drill bits are used in cutting applications where high cutting speeds are traditionally used, and where the material has a tendency to gall on the bit or otherwise clog the hole, such as aluminum or copper. A fast spiral (high twist rate or "compact flute") drill bit is used in high feed rate applications under low spindle speeds, where removal of a large volume of chips is required. The spiral (or rate of twist) in the drill bit controls the rate of chip removal.Drill geometry has several characteristics:
